The production of grass pellets is a vital process in the biomass energy sector and animal feed industry, providing a renewable and efficient source of energy and nutrition. The efficiency of a grass pellet machine plays a significant role in determining the quality of the final product. This article explores the relationship between production efficiency and product quality, highlighting the key factors that influence both aspects.
1. Understanding Production Efficiency
Production efficiency refers to the ability of a grass pellet machine to convert raw materials into finished pellets with minimal waste, optimal energy consumption, and consistent quality. High production efficiency means that the machine can produce a larger quantity of pellets in a shorter amount of time while maintaining the desired quality standards. Key indicators of production efficiency include:
- Output Rate: The amount of grass pellets produced per hour.
- Energy Consumption: The amount of energy used to produce a given quantity of pellets.
- Downtime: The time the machine is not operational due to maintenance or breakdowns.
2. The Role of Raw Material Quality
The quality of raw materials used in the pellet production process significantly impacts both production efficiency and product quality. Grass quality, moisture content, and particle size are critical factors to consider.
- Moisture Content: The ideal moisture content for grass pellets is typically between 10% and 15%. If the moisture content is too high, it can lead to poor pellet formation and increased energy consumption during the pelleting process. Conversely, if the moisture content is too low, it may result in weak pellets that break easily.
- Particle Size: The size of the grass particles affects how well they can be compacted into pellets. Finer particles generally lead to better pellet quality, as they allow for more uniform mixing and improved binding during the pelleting process. However, excessively fine particles can increase friction and energy consumption, negatively impacting production efficiency.
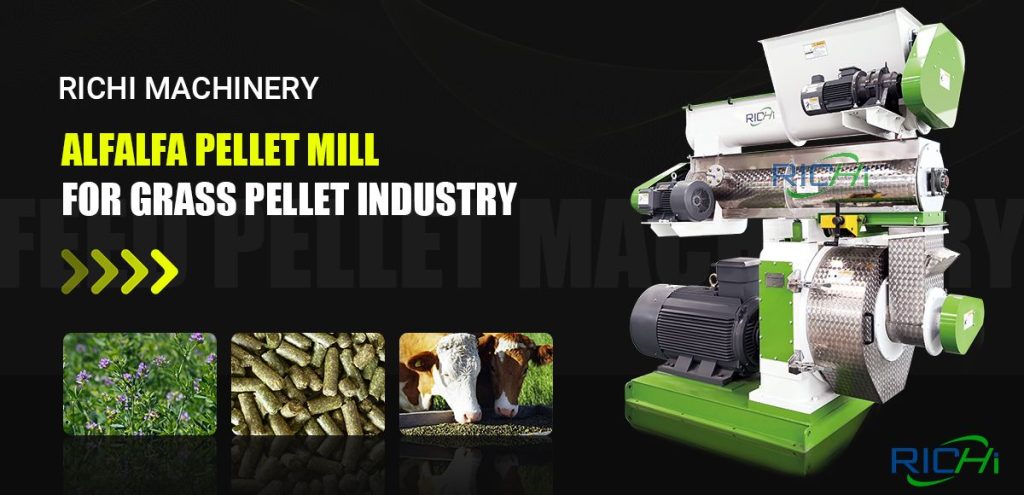
3. Impact of Machine Design on Efficiency and Quality
The design of the grass pellet machine itself plays a crucial role in determining both production efficiency and product quality.
- Pellet Mill Type: The type of pellet mill used can significantly affect the efficiency of the production process. Ring die pellet mills are generally more efficient for large-scale production, providing higher output rates and better pellet quality compared to flat die mills. The design of the die and rollers also influences the compression process, affecting pellet density and durability.
- Conditioning System: An effective conditioning system is essential for preparing the grass mixture for pelleting. Conditioning involves adding steam and moisture to the feedstock, which helps to gelatinize starches and improve binding. A well-designed conditioning system can enhance the production efficiency of the pellet mill and result in higher-quality pellets.
4. Energy Consumption and Its Effects
Energy consumption is a critical factor in assessing the efficiency of a grass pellet machine. High energy consumption can lead to increased production costs and reduced profitability.
- Energy-Efficient Components: Using energy-efficient motors and components can help reduce energy consumption during the pelleting process. This not only lowers operational costs but also minimizes environmental impact.
- Impact on Pellet Quality: Excessive energy consumption can indicate inefficiencies in the production process, such as poor machine design or incorrect settings. These inefficiencies can lead to variations in pellet quality, such as inconsistent size, density, and durability.
5. Downtime and Maintenance
Downtime due to maintenance or breakdowns can significantly affect both production efficiency and product quality.
- Preventive Maintenance: Implementing a preventive maintenance program can help minimize downtime and ensure that the machine operates at peak efficiency. Regular inspections, lubrication, and timely replacement of worn components are essential for maintaining optimal performance.
- Impact on Product Quality: Frequent breakdowns or maintenance issues can lead to inconsistent production schedules, resulting in variations in feedstock quality and processing conditions. This inconsistency can adversely affect the quality of the final pellets.
6. Monitoring and Control Systems
Advanced monitoring and control systems play a vital role in optimizing production efficiency and ensuring consistent product quality.
- Real-Time Monitoring: Implementing real-time monitoring systems allows operators to track key performance indicators (KPIs) such as production output, energy consumption, and pellet quality. This data can be used to make informed decisions and adjustments to optimize the production process.
- Automated Control Systems: Automated control systems can help regulate parameters such as temperature, pressure, and moisture content during the pelleting process. Maintaining these parameters within optimal ranges is crucial for achieving high-quality pellets.
7. Quality Control Measures
Establishing effective quality control measures is essential for ensuring that the pellets produced meet the desired specifications.
- Regular Testing: Conducting regular tests on the pellets for parameters such as moisture content, density, and durability is crucial for maintaining quality standards. This testing should be integrated into the production process to identify issues early and make necessary adjustments.
- Feedback Loops: Implementing feedback loops that allow operators to receive immediate information about pellet quality can help identify trends and areas for improvement. This proactive approach can enhance production efficiency and product quality. (Related post: alfalfa pellet machine)
Conclusion
The production efficiency of a grass pellet machine is closely linked to the quality of the pellets produced. Factors such as raw material quality, machine design, energy consumption, downtime, and monitoring systems all play a significant role in determining both efficiency and quality. By focusing on optimizing these factors, manufacturers can enhance the production process, reduce costs, and ensure that the pellets meet the nutritional and energy needs of their intended applications.Investing in high-quality machinery, implementing effective maintenance programs, and establishing robust quality control measures will contribute to the overall success of grass pellet production. As the demand for renewable energy sources and high-quality animal feed continues to grow, understanding the relationship between production efficiency and product quality will be essential for maintaining a competitive edge in the market.