Introduction to Fish Feed Making Machine
In the expanding realm of aquaculture, the fish feed making machine has emerged as a pivotal tool. Primarily designed to produce customized fish feed, these machines cater to the specific dietary requirements of various fish species. This apparatus functions by combining raw materials such as fish meal, soybean, and other additives into a homogenized feed. The intricate process ensures that the nutrients remain intact while enhancing the palatability and digestibility of the feed.
The primary purpose of a fish feed making machine is to produce high-quality feed that supports the healthy growth and development of fish. By tailoring the feed composition to meet the biological needs of specific fish, these machines help aquaculture farmers optimize their fish farming operations. Quality feed is instrumental in achieving higher growth rates, better resistance to diseases, and improved overall fish health, which ultimately leads to a more profitable and sustainable aquaculture business.
At the heart of the fish feed making process is a series of well-coordinated mechanisms. These include grinding, mixing, conditioning, extrusion, and drying. Initially, the raw materials are finely ground to enable thorough mixing and conditioning. During extrusion, the feed is subjected to high temperatures and pressures, which not only shape the pellets but also eliminate any potential pathogens. The drying phase ensures the removal of moisture, thus extending the shelf life of the feed.
In the context of the aquaculture industry, the utility of the fish feed making machine cannot be overstated. It fosters the production of nutritional, environmentally sustainable, and economically viable feed options. As the global demand for fish and seafood continues to rise, these machines stand out as essential contributors to the efficiency and scalability of fish farming operations.
Uses of Fish Feed Making Machine
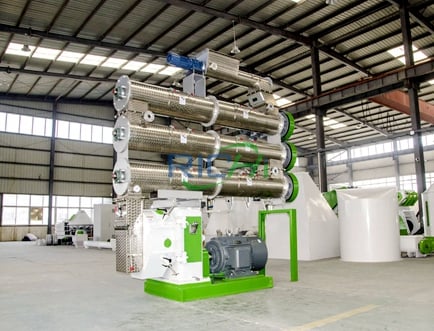
Fish feed pellet machines are instrumental in the aquaculture industry, serving a crucial role in producing a variety of fish feed tailored to different species and growth stages. These machines are designed to manufacture pelletized or extruded feed, which can range from starter crumbles to grower pellets, ensuring optimal nutrition tailored to the specific dietary needs of fish. The ability to control the size, shape, and composition of the pellets is a significant advantage, as it allows aquaculturists to cater precisely to the nutritional requirements of various fish species.
One of the primary benefits of utilizing fish feed making machines is the enhanced nutritional content of the feed. These machines allow for the precise measurement and incorporation of essential vitamins, minerals, proteins, and other nutrients vital for fish growth and health. Custom formulations can be produced to meet the specific needs of different species, thereby enhancing growth rates, improving feed conversion ratios, and reducing overall production costs. The consistency and quality of the feed produced using these machines can prevent potential health issues and promote the well-being of the fish.
Fish feed making machines offer efficiency in terms of production scale and speed, making them particularly advantageous in commercial aquaculture systems. With the ability to produce large quantities of feed in a relatively short period, these machines can significantly reduce labor and operational costs. Additionally, the automation and mechanization provided by these machines save valuable time, allowing fisheries to focus on other critical aspects of their operations. This efficiency is beneficial not only for large-scale commercial operations but also for small and medium-sized enterprises looking to streamline their feed production processes.
Furthermore, fish feed making machines are advantageous in regions where the procurement of commercial feed is challenging or costly. By enabling local production of high-quality fish feed, these machines can support sustainable aquaculture practices and local economies. They provide the flexibility to utilize locally sourced ingredients, which can further reduce costs and promote resource efficiency.
Industry Application Analysis with Specific Data
Fish feed making machines play a pivotal role in aquaculture, fueling the industry’s growth by enhancing production efficiency and economic viability. Their application is widespread, with significant impact across different scales of fish farming operations. According to recent data, the global aquaculture feed market reached a valuation of $67.1 billion in 2021, highlighting the crucial role of feed manufacturing equipment. The mechanization of feed production facilitates the creation of high-quality, nutrient-rich pellets that contribute to the health and growth of fish, ultimately improving yields and profitability for fish farmers.
Production volumes within the fish feed industry have also seen a remarkable increase. For instance, data from a 2020 industry report indicates that automated feed production lines have boosted output by approximately 15-20% compared to traditional methods. The adoption of fish feed making machines has been attributed to a reduction in labor costs, better control over ingredient ratios, and more consistent pellet sizes, which are essential for the optimal feeding of various fish species.
Economic benefits derived from these machines extend beyond mere production enhancements. A case study involving a medium-sized aquaculture operation in Southeast Asia illustrated that investing in a fish feed making machine reduced feed wastage by up to 25%. This efficiency not only staved off significant financial losses but also aligned with sustainable practices, minimizing environmental impact through the effective use of resources.
Additional case studies underline success stories such as a large-scale fish farm in Norway that shifted to automated feed production. The move led to a 30% increase in productivity within the first year, underscoring the potential for significant economic gain through strategic investment in technology. As aquaculture continues to expand, the utilization of fish feed making machines is poised to become even more integral, driving industry standards towards higher efficiency and sustainability.
Classification of Fish Feed Making Machines
Fish feed making machines are essential equipment in the aquaculture industry, helping producers generate high-quality fish feed to meet the specific nutritional requirements of different fish species. These machines can broadly be classified into two main categories: extruders and pellet mills. Each type has distinct features that cater to different production needs.
Extruders are designed to produce various sizes, textures, and shapes of fish feed, making them highly versatile. They work by pushing a mixture of ingredients through a rotating screw under high pressure, which then exits through a die forming feed pellets. Key components of an extruder include the barrel, screw, and die. One of the main benefits of using an extruder is the ability to create floating pellets, which are especially beneficial for surface-feeding fish species.
Pellet mills, on the other hand, are generally used to produce sinking fish feed. They function by compressing powdered feed ingredients through a die under high pressure, forming dense pellets. Key components of a pellet mill include the roll, die, and knife assembly. The compact nature of the pellets ensures that the feed is less susceptible to breakage and nutrient loss during handling and transportation. Pellet mills are ideal for producing large volumes of uniform pellets, catering to the needs of commercial fish farms.
While extruders can accommodate a wider range of raw materials and produce a more diverse array of pellet types, pellet mills offer a simpler design with lower operational costs and maintenance requirements. Selecting the appropriate fish feed making machine depends on various factors including the species of fish being farmed, the scale of production, and specific nutritional needs.
Understanding the key components and functions of these machines can significantly aid producers in optimizing their fish feed production processes. Each machine type provides unique advantages, thereby contributing to the efficiency and effectiveness of aquaculture operations.
Working Principle of Fish Feed Making Machines
Fish feed making machines are specialized equipment designed to produce high-quality feed for aquatic animals. The operation of these machines begins with the intake of raw materials such as fish meal, soybean meal, corn, and various nutrients. These ingredients are first ground into a fine powder through the grinding mill, ensuring uniform particle size which is essential for the subsequent processing steps.
Once the raw materials are uniformly ground, they are transferred to the mixing chamber. In this stage, ingredients are thoroughly mixed to attain a homogeneous blend, which is crucial for producing consistent and nutritionally balanced fish feed. Precise mixing ensures that every pellet contains a proportionate amount of nutrients.
The mixed material is then fed into the extruder or pelletizer, the pivotal component of a fish feed making machine. Here, the material undergoes extrusion or pelletization, which involves mechanical and thermal processing. During extrusion, the material is forced through a die under intense pressure and heat. This process not only shapes the feed into specific sizes but also cooks the ingredients, enhancing their digestibility and binding properties.
Key parameters such as temperature, pressure, and moisture content are meticulously controlled during extrusion to achieve optimal feed quality. Higher temperatures and pressures typically enhance protein denaturation and starch gelatinization, which are critical for the palatability and stability of the feed when in water.
After extrusion, the fish feed passes through a cooling and drying system. The freshly extruded pellets are moist and warm, requiring cooling to solidify the structure and reduce moisture content. The drying phase reduces moisture further, ensuring the feed has a long shelf life and resists spoilage.
The final step is the screening and packaging. The feed is sifted to remove fines and ensure uniform pellet size, then packaged for storage and distribution. Efficient operation of the fish feed making machine is paramount to producing high-quality feed that meets the nutritional needs of aquatic species.
Process Flow in Fish Feed Production
The production of high-quality fish feed through a fish feed making machine is a meticulous process involving several critical stages, each contributing to the final product. The initial stage begins with raw material handling. Raw materials, such as fish meal, soybean meal, and grain, are carefully selected and inspected to ensure they meet the nutritional requirements for fish. These materials are cleaned to remove impurities that could affect the feed quality.
Following the procurement and cleaning of the raw materials, we move to conditioning. During conditioning, steam and water are introduced to the raw materials to adjust their moisture content and temperature. This is crucial as it prepares the materials for better mixing and extrusion while ensuring the feed’s nutritional value is preserved.
The next stage, mixing, combines various raw materials uniformly to create a balanced nutritional profile. The importance of this stage cannot be overstated as it ensures each pellet produced contains the right proportions of the ingredients. Advanced mixers are employed to achieve a homogeneous blend, reducing the risk of segregation.
Once mixed, the blend proceeds to extrusion or pelletization. During this stage, the fish feed making machine subjects the mixture to high pressure and temperature, transforming it into uniform pellets. Extrusion/pelletization not only shapes the feed but also improves its digestibility and shelf life by breaking down certain complex protein structures.
Post-extrusion, the pellets enter the drying phase. This step removes excess moisture from the pellets, bringing them to the optimal moisture level required for storage and transportation. Effective drying is essential to prevent mold growth and ensure the feed’s longevity.
Subsequently, the pellets undergo cooling. The cooling process is vital because it reduces the temperature of the pellets, which have been elevated by the extrusion and drying processes. Proper cooling stabilizes the physical structure of the pellets, preventing them from crumbling during handling.
The final stage in the fish feed production process is packaging. The dried and cooled pellets are packed in moisture-proof, durable bags or containers to preserve their quality during storage and distribution. Proper packaging ensures the feed reaches the end-users with its nutritional integrity intact.
Each stage in the process flow, from raw material handling to packaging, plays a pivotal role in producing high-quality fish feed, underscoring the importance of using a reliable fish feed making machine to achieve optimal results. Related content: https://www.richimanufacture.com/floating-fish-feed-production-line/
Choosing the Right Fish Feed Making Machine and Supplier
When selecting a fish feed making machine, several factors must be considered to ensure an optimal match for your production needs. One of the primary considerations is production capacity. It is essential to assess the volume of feed required daily or weekly and choose a machine that can consistently meet those demands without compromising on quality or efficiency. Various machines cater to different production scales, from small-scale operations to large commercial enterprises; thus, alignment with your operational size is critical.
Another key element is the type of feed you plan to produce. Fish feed can vary significantly in composition, buoyancy, size, and nutritional content, depending on the species of fish and their growth stages. Ensure that the fish feed making machine you select is versatile enough to handle these variations, particularly if your business involves producing different types of feed. Features such as adjustable pellet size, ingredient mix options, and ease of cleaning and maintenance can greatly enhance flexibility and operational smoothness.
Equally important is the selection of a reliable supplier. A reputable supplier will provide machines of high quality, backed by warranties and certifications that attest to their durability and safety standards. Furthermore, a good supplier should offer robust customer support, including technical assistance, troubleshooting, and maintenance services. This support is indispensable for minimizing downtimes and ensuring the longevity of your machinery.
Customization capabilities also play a pivotal role in the supplier selection process. Your fish feed production line may need to be tailored to fit specific site layouts and project requirements. A supplier that can customize and optimize the machine setup will save you significant time and resources while maximizing efficiency. This customization may involve modifications to the machinery or the design of ancillary systems such as conveyors, mixers, and storage units.
Additionally, consider suppliers who exhibit a strong track record of reliability and customer satisfaction. Reviews, testimonials, and case studies can provide valuable insights into the supplier’s performance and commitment to quality. By prioritizing these factors, you not only ensure the acquisition of a dependable fish feed making machine but also establish a partnership that supports sustainable production and business growth.
Introducing Richi Machinery and Its Capabilities
Richi Machinery stands at the forefront as a leading manufacturer located in Henan, China, renowned for its unwavering commitment to excellence in the realm of pellet production lines. With years of accumulated experience, Richi Machinery has carved out a niche by providing bespoke solutions that precisely meet the unique needs of each customer, particularly in the aquaculture industry. This underscores their expertise in site design and execution of turnkey projects, making them a trusted partner for any business looking to optimize its fish feed production processes.
One of Richi Machinery’s most notable strengths lies in its ability to customize fish feed making machines. Recognizing that no two customers’ requirements are alike, the company excels in tailoring their equipment to match specific production goals, raw material availability, and operational constraints. This level of customization ensures that the final product effectively meets the rigorous standards of feed quality and production efficiency that modern aquaculture demands.
Moreover, Richi Machinery’s expertise doesn’t stop at machinery production. Their seasoned team is adept at providing comprehensive site design services, ensuring that each piece of equipment is integrated seamlessly into the customer’s overall production setup. This holistic approach not only enhances workflow efficiency but also minimizes potential bottlenecks, setting the stage for a highly productive and cost-effective operation.
Turnkey project execution is another hallmark of Richi Machinery. They offer end-to-end solutions, from initial consultation and equipment design to installation, testing, and after-sales support. This all-encompassing service model ensures that customers receive a fully operational production line, ready to deliver optimum performance from day one.
In summary, Richi Machinery’s rich experience, bespoke machine customization capabilities, and comprehensive service offerings make them an ideal partner for businesses aiming to scale their fish feed production effectively. Whether you’re starting a new production line or upgrading your existing setup, Richi Machinery provides the expertise and support needed to achieve your goals.
Practical Application Value of Fish Feed Making Machines
In the aquaculture industry, the utilization of fish feed making machines distinctly enhances various facets of aquaculture operations. Primarily, these machines contribute significantly to the improvement of feed quality. Fish feed making machines enable precise formulation and production of feed, ensuring a balanced nutritional profile tailored to specific fish species. By employing sophisticated extrusion and pelletizing technologies, they can deliver consistent feed sizes and textures that maximize feed intake and minimize waste.
Economic efficiency is another pivotal advantage offered by fish feed making machines. By producing feed in-house, fish farmers can substantially reduce their reliance on commercial feed suppliers, thereby lowering operational costs. The ability to adjust recipes and ingredients based on seasonal availability and market prices further optimizes cost-efficiency. Consequently, farmers are better positioned to achieve higher profitability, as feed expenses constitute a significant portion of overall production costs in aquaculture.
Scalability is a crucial factor for growth-oriented aquaculture enterprises. Fish feed making machines are designed to cater to diverse production scales, providing flexibility to both small-scale operations and large, commercial fish farms. As production demands increase, these machines can accommodate higher output rates without compromising feed quality. This scalability ensures that farmers can expand their operations seamlessly, meeting market demands and business growth aspirations.
Sustainability is an ever-growing concern in modern aquaculture. Fish feed making machines play an essential role in advancing sustainable practices by facilitating the use of alternative ingredients. Rather than relying heavily on traditional fishmeal and fish oil, which are often unsustainable, these machines can incorporate plant-based proteins and other eco-friendly ingredients. This shift not only reduces the environmental impact but also supports the long-term viability of aquaculture activities.
Real-world examples underscore the transformative impact of adopting fish feed making machines. Farmers have reported substantial improvements in feed conversion ratios, resulting in faster growth rates and healthier fish populations. Testimonials highlight reductions in feed costs by as much as 20%, alongside an enhanced ability to produce specialized feeds for different growth stages and species.
In summary, the integration of fish feed making machines into aquaculture practices yields tangible benefits. From superior feed quality and economic gains to scalable production and sustainable operations, these machines prove indispensable in driving the industry forward.