Constructing a large-scale feed mill plant is a complex and significant undertaking that requires meticulous planning and execution. A well-designed feed mill is vital for producing high-quality animal feed to meet the increasing demands of the agricultural sector. This guide outlines the critical steps involved in establishing a large-scale feed mill plant, ensuring every aspect is thoroughly considered for a successful operation.
1. Conduct Thorough Market Research
Before initiating the construction of a complete feed mill plant, conducting extensive market research is crucial:
- Demand Analysis: Evaluate the local and regional demand for various types of animal feed, such as poultry, cattle, and aquaculture feed. Understanding current market trends will help you determine the appropriate scale of your operation.
- Competition Assessment: Analyze existing feed mills in the area to understand their strengths and weaknesses. This will help you develop a competitive edge and identify opportunities for differentiation.
- Regulatory Considerations: Familiarize yourself with local regulations related to feed production, including safety standards, environmental laws, and licensing requirements.
2. Develop a Robust Business Plan
A well-crafted business plan serves as a blueprint for the development of the feed mill:
- Financial Projections: Estimate the initial capital investment required for construction, equipment procurement, and operational costs. Include financial projections covering revenue, profit margins, and return on investment.
- Operational Strategy: Outline the entire production process, from raw material sourcing to feed production and distribution. Define your supply chain, logistics, and production methods.
- Marketing Plan: Develop a comprehensive marketing strategy to promote your feed products, build brand recognition, and establish relationships with farmers, distributors, and other stakeholders.
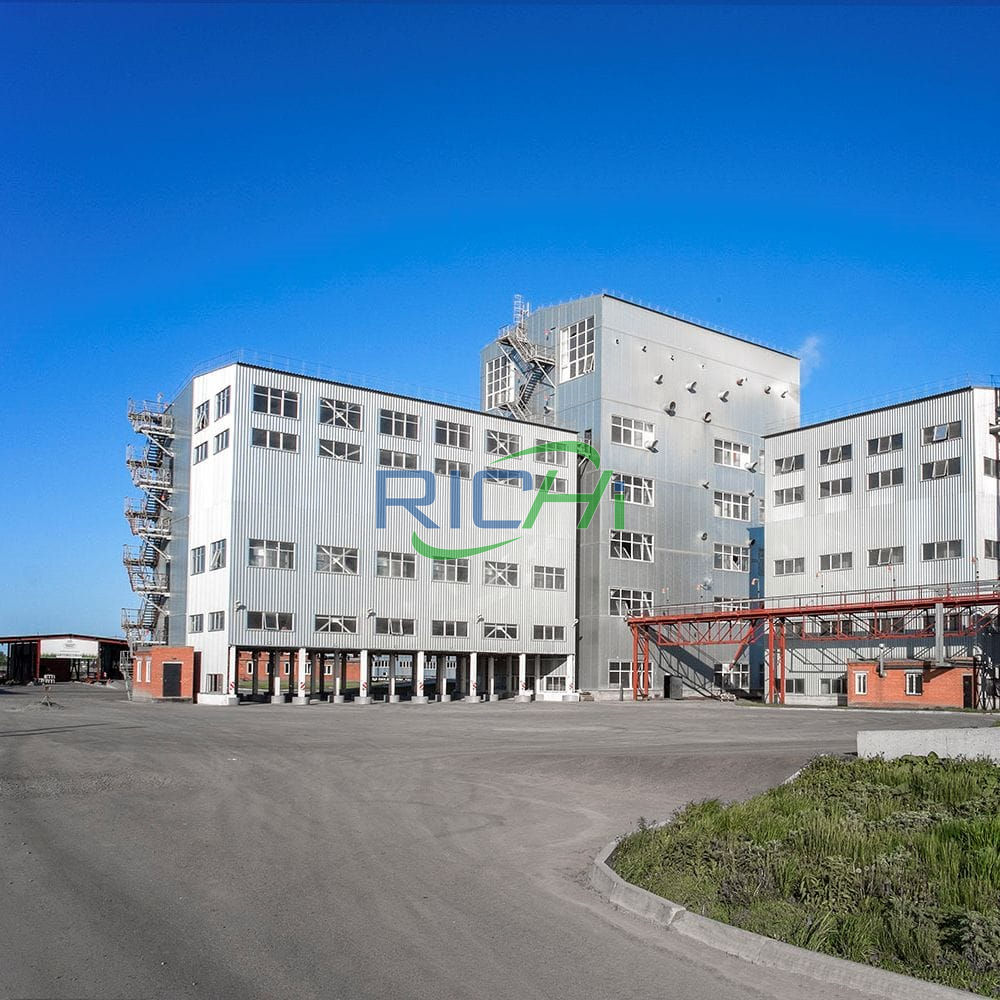
3. Design an Efficient Plant Layout
An effective layout is crucial for ensuring efficient operations within the feed mill:
- Material Flow: Design the plant layout to facilitate smooth and efficient material flow throughout the production process, from raw material intake to final product packaging.
- Zoning: Allocate distinct areas for each stage of production, including raw material storage, grinding, mixing, pelleting, cooling, and packaging. Ensure that each area is appropriately sized for the intended production capacity.
- Safety and Compliance: Incorporate necessary safety measures into the design, such as fire safety systems, adequate ventilation, and waste management solutions, ensuring compliance with local regulations.
4. Select Appropriate Equipment and Machinery
Choosing the right equipment is essential for the plant’s efficiency and the quality of the feed produced:
- Feed Processing Equipment: Select high-capacity machines for grinding, mixing, pelleting, cooling, and packaging that match your production requirements.
- Automation: Invest in automation systems to enhance production efficiency, reduce labor costs, and improve product consistency. Automation also helps in monitoring and controlling the production process.
- Quality Control: Integrate quality control equipment, such as moisture meters and particle size analyzers, to ensure that your feed meets industry standards.
5. Obtain Required Permits and Licenses
Securing all necessary permits and licenses before construction begins is crucial:
- Construction Permits: Apply for construction permits, including zoning approvals and environmental impact assessments.
- Operational Licenses: Obtain the necessary licenses to operate the feed mill, which may include health and safety certifications and adherence to food safety regulations.
- Environmental Permits: Ensure compliance with environmental regulations related to waste disposal, emissions, and noise control.
6. Begin Construction of the Feed Mill
With all preparations complete, commence the construction phase:
- Contracting: Engage a reputable construction contractor with experience in agricultural facility construction. Ensure they understand the specific requirements of building a feed mill.
- Timeline Management: Establish a detailed timeline for the construction project, including key milestones. Regularly monitor progress to ensure the project stays on schedule.
- Quality Assurance: Implement quality control measures throughout the construction process to ensure that all materials and workmanship meet the required standards.
7. Install and Commission Equipment and Machinery
Once construction is complete, proceed with the installation of equipment:
- Professional Installation: Hire skilled technicians to install all machinery, ensuring each piece is set up according to the manufacturer’s specifications.
- Testing and Calibration: Thoroughly test and calibrate all equipment to ensure it functions correctly before full-scale production begins.
- Staff Training: Provide comprehensive training for your staff on operating the machinery and understanding the production process, ensuring both safety and efficiency.
8. Implement Rigorous Quality Control Measures
Establish robust quality control protocols to maintain the high standard of your feed products:
- Standard Operating Procedures (SOPs): Develop and enforce SOPs for every stage of the production process, from raw material handling to final product packaging.
- Regular Testing: Implement routine testing of raw materials and finished products to ensure they meet nutritional standards and safety regulations.
- Feedback Mechanism: Set up a system for gathering feedback from customers and staff to continually improve product quality and operational efficiency.
9. Launch Production
With everything in place, it’s time to start production:
- Initial Production Runs: Begin with small-scale production runs to test equipment and processes, making any necessary adjustments to optimize performance.
- Marketing and Distribution: Start marketing your feed products to local farmers and distributors. Establish efficient distribution channels to ensure timely delivery of your products.
- Continuous Improvement: Regularly assess production performance, seeking opportunities to enhance efficiency, product quality, and customer satisfaction.
10. Monitor and Optimize Operations
Continuous monitoring and optimization are key to sustaining successful operations:
- Performance Metrics: Track key performance indicators such as production volume, energy consumption, and waste generation. Use this data to identify areas for improvement.
- Regular Maintenance: Implement a proactive maintenance schedule for all equipment to minimize downtime and ensure consistent production.
- Adapt to Market Changes: Stay informed about market trends and customer preferences. Be prepared to adjust your product offerings and production processes to meet evolving demands.
Conclusion
Building a large-scale feed mill factory requires careful planning, substantial investment, and diligent execution. By following these steps—ranging from market research and business planning to selecting the right equipment and optimizing operations—you can establish a successful feed mill operation.
As the demand for high-quality animal feed continues to grow, investing in a well-designed feed mill can position your business for success in the competitive agricultural market. With the right approach, your feed mill can significantly contribute to the efficiency and sustainability of animal farming in your region.
For details please contact: pellet maker machine
WhatsApp:86 138 3838 9622
Email:enquiry@richipelletmachine.com