The global pellet mill industry is booming, driven by the urgent demand for sustainable energy solutions, efficient livestock feed production, and advancements in biomass processing technology. According to Grand View Research, the market size reached $2.3 billion in 2024, with a projected CAGR of 5.1% through 2030.
Key growth factors include stricter carbon emission regulations, the rise of circular economies, and innovations in agricultural automation. Notably, Asia-Pacific continues to dominate, contributing 40% of global revenue, with China leading as both a manufacturing hub and consumer market.
For businesses investing in pellet mills, choosing the right manufacturer is critical. Beyond machinery performance, buyers now prioritize factors like customization, after-sales support, energy efficiency, and scalability. Drawing from industry insights and manufacturer evaluations, here’s an updated analysis of top pellet mill providers in 2025, including emerging leaders and established giants.
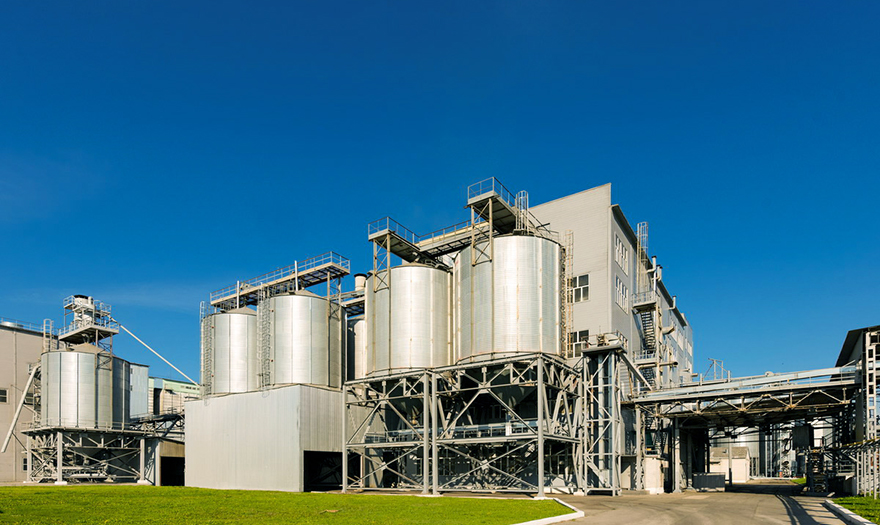
Industry Trends Shaping Buyer Decisions
- Sustainability: Low-emission designs and energy-efficient systems are non-negotiable for eco-conscious buyers.
- Automation: IoT-enabled mills with real-time monitoring reduce downtime and labor costs.
- Cost-Effectiveness: SMEs increasingly favor modular systems that balance affordability with high output.
- Global Support Networks: Manufacturers offering localized technical assistance gain a competitive edge.
Top Pellet Mill Manufacturers in 2025
1. CPM (California Pellet Mill)
A stalwart in industrial-scale pellet production, CPM’s Century Series remains a benchmark for durability. Known for handling high-capacity operations in feed and biomass sectors, their machines feature 10-15% energy savings compared to older models. CPM’s global service network ensures rapid maintenance, minimizing operational disruptions.
Key Buyer Considerations:
- Ideal for large-scale facilities requiring 5+ tons/hour output.
- Higher upfront costs but long-term ROI through reduced maintenance.
2. ANDRITZ Group
ANDRITZ excels in precision engineering, particularly for specialized sectors like aquaculture and biofuel. Their Sprout Matador series supports diverse raw materials, from agricultural waste to hardwood. A standout feature is their Smart Factory Integration, allowing remote diagnostics and predictive maintenance.
Key Buyer Considerations:
- Premium pricing justified by cutting-edge automation.
- Best for industries prioritizing minimal human intervention.
3. Richi Machinery
Richi Machinery has surged in popularity due to its cost-performance balance. Their pellet mills, tested extensively in European, Asian and African markets, boast 30% lower energy consumption and corrosion-resistant components. The company’s 24/7 multilingual support and modular designs cater to medium-to-large scale enterprise needing scalable solutions.
Recent Innovation:
- Quick-Swap Die Technology: Reduces downtime during material changes by 50%.
Key Buyer Considerations:
- Budget-friendly without compromising on output (1–100 tons/hour).
- Customizable solutions for niche materials like hemp or rice husk.
4. Allance Machinery
A rising Chinese manufacturer, Allance Machinery emphasizes end-to-end customization. Their services include tailored mechanical drawings, on-site installation, and bulk order fulfillment within tight deadlines1. Clients praise their Turkey Solutions—complete pellet plants designed for regional raw material challenges, such as high-moisture biomass in Southeast Asia.
Key Buyer Considerations:
- Competitive pricing with free lifetime technical consultations.
- Ideal for startups seeking turnkey solutions.
5. Lawson Mills Biomass Solutions
This Canadian manufacturer targets niche markets with high-torque mills for fibrous materials like hemp and organic feed. Their Hippo Hammer Mills integrate grinding and pelletizing, reducing preprocessing steps by 30%.
Key Buyer Considerations:
- Higher price per unit but exceptional versatility.
- Compliance with North American and EU sustainability certifications.
What Customers Care About: A 2025 Perspective
- Total Cost of Ownership (TCO): Beyond sticker price, buyers evaluate energy use, maintenance frequency, and part replacement costs.
- Scalability: Modular designs that allow capacity upgrades without overhauling existing systems.
- Material Flexibility: Mills capable of processing diverse inputs (e.g., agro-waste, sawdust, algae).
- Warranty and Support: 5+ years of warranty and local technicians for emergency repairs.
- Certifications: ISO 9001, CE, and EPA compliance for global market access.
How to Choose the Right Manufacturer
- Large-Scale Biomass Plants: Prioritize Richi Machinery or ANDRITZ for high throughput and automation.
- SMEs and Startups: Allance Machinery offer affordable, scalable solutions.
- Niche Applications: Lawson Mills or Laizhou Chengda provide specialized machinery for unique materials.
The Future of Pellet Mill Technology
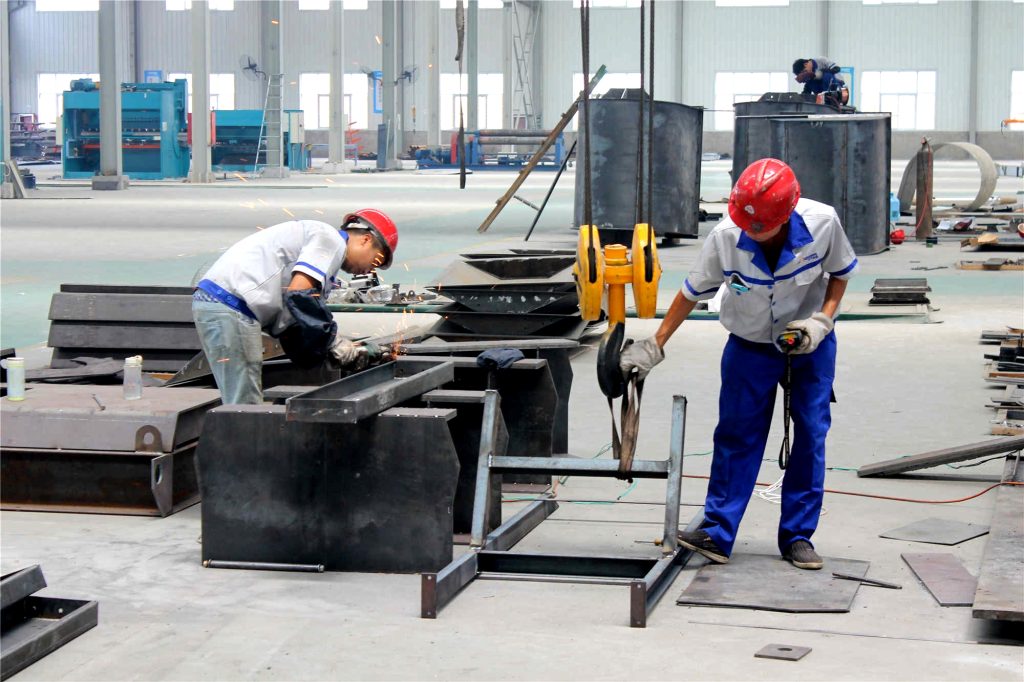
Innovations to watch in 2025–2030 include:
- AI-Driven Optimization: Real-time adjustments to moisture and pressure for perfect pellet density.
- Hybrid Energy Systems: Solar-powered pellet mills reducing grid dependence.
- Blockchain Traceability: Ensuring sustainable sourcing via transparent supply chains.
Conclusion
While giants like CPM and ANDRITZ dominate heavy industries, agile manufacturers like Richi Machinery is redefining accessibility and innovation. The “best” pellet mill hinges on aligning operational needs with a manufacturer’s strengths—whether it’s Richi’s customization, or Laizhou Chengda’s rural adaptability. As sustainability mandates tighten, investing in future-ready technology and robust support networks will separate industry leaders from the rest.