The production of bagasse pellets has gained traction as a sustainable solution for biomass energy and animal feed. Bagasse, the fibrous residue left after sugarcane processing, is an abundant and renewable resource. However, to ensure profitability and sustainability, it is essential to optimize the production process of bagasse pellet machines. This article discusses various strategies to enhance efficiency, reduce costs, and improve the overall production process.
1. Understanding the Production Process
Before delving into optimization strategies, it is crucial to understand the typical production process of bagasse pellets, which involves several key steps:
- Raw Material Preparation: This includes collecting, drying, and grinding the bagasse to achieve the required particle size.
- Conditioning: The ground bagasse is conditioned with steam or moisture to improve binding properties before pelleting.
- Pelleting: The conditioned material is compressed through a pellet mill die to form pellets.
- Cooling and Screening: The hot pellets are cooled and screened to remove fines and ensure uniform size.
- Packaging: The final product is packaged for storage or distribution.
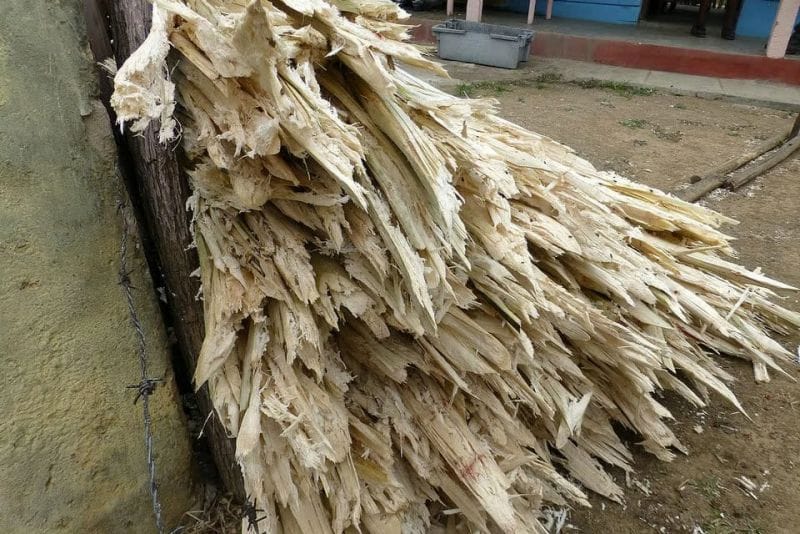
2. Raw Material Optimization
The quality and preparation of raw materials significantly impact production efficiency and costs.
- Moisture Content Management: The ideal moisture content for bagasse pellets is typically between 10% and 15%. Maintaining this moisture level is crucial for optimal pelleting. If the bagasse is too wet, it can lead to poor pellet quality and increased energy consumption. Conversely, if it is too dry, it may not bind effectively. Implementing a moisture monitoring system can help maintain the desired levels.
- Particle Size Reduction: The particle size of the raw material affects the pelleting process. Using a hammer mill or grinder to achieve a consistent particle size can enhance the efficiency of the pellet mill. Finer particles generally lead to better binding and higher-quality pellets, but excessive fineness can increase energy consumption. Therefore, optimizing the grinding process is essential.
3. Conditioning Process Enhancement
Conditioning is a critical step that prepares the bagasse for pelleting and significantly impacts pellet quality and production efficiency.
- Steam Conditioning: Using steam during the conditioning process can improve the gelatinization of starches and enhance the binding properties of the bagasse. This leads to higher-quality pellets that are less likely to break during handling. Adjusting the steam temperature and conditioning time can optimize this process.
- Moisture Addition: In addition to steam, adding a small amount of water can improve pellet quality. However, it is essential to monitor the moisture levels carefully to avoid over-saturation.
4. Pellet Mill Optimization
The performance of the pellet mill is crucial for maximizing production efficiency.
- Die and Roller Maintenance: Regular maintenance and inspection of the die and rollers are essential for ensuring optimal performance. Worn or damaged components can lead to reduced output and increased energy consumption. Implementing a preventive maintenance schedule can help identify and address issues before they escalate.
- Adjusting Operating Parameters: The operating parameters of the pellet mill, such as pressure and temperature, should be regularly monitored and adjusted based on the specific characteristics of the bagasse being processed. Fine-tuning these parameters can lead to improved pellet quality and reduced energy consumption.
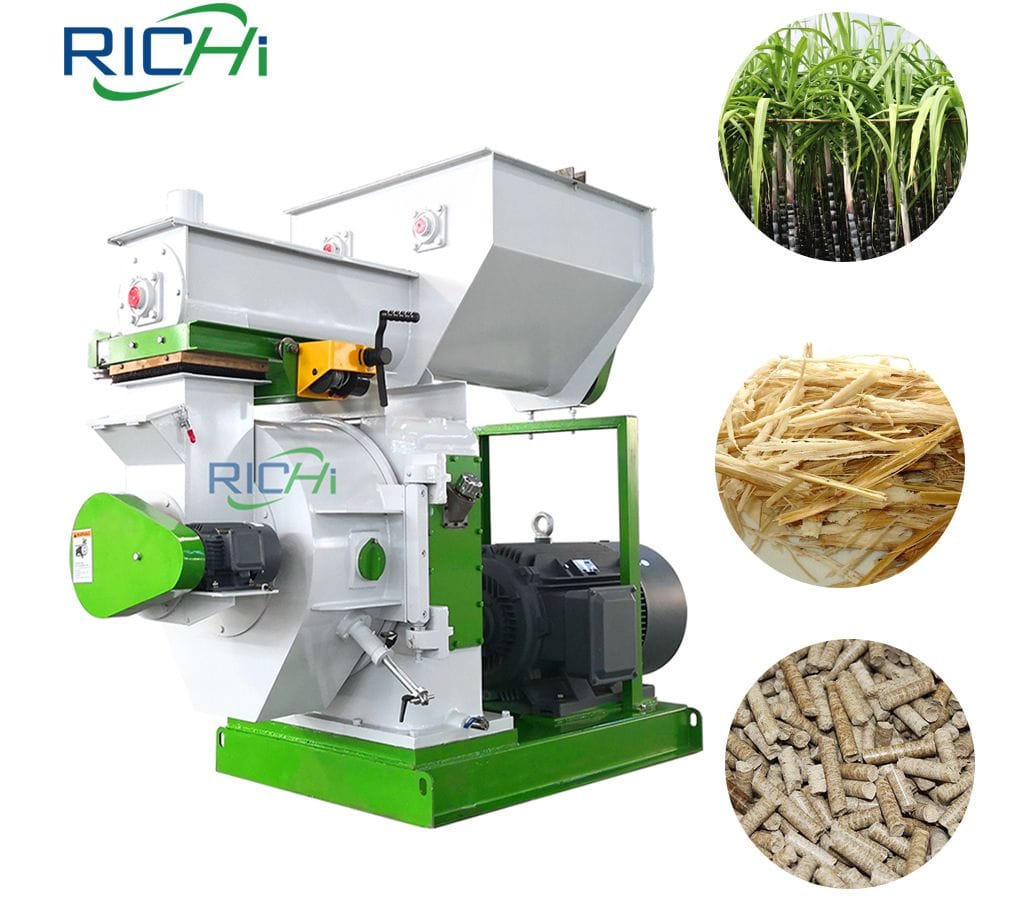
5. Energy Efficiency Improvements
Energy consumption is a significant cost factor in the production of bagasse pellets. Implementing energy-efficient practices can lead to substantial cost savings.
- Energy-Efficient Motors: Upgrading to high-efficiency motors can reduce energy consumption in the pellet mill and other machinery. While the initial investment may be higher, the long-term savings on energy costs can offset this expense.
- Heat Recovery Systems: Installing heat recovery systems can capture excess heat generated during the pelleting process and reuse it for conditioning or other purposes. This reduces the overall energy demand and improves efficiency. (Related post: biomass pellet machine for sale)
6. Cooling and Screening Optimization
The cooling and screening processes are essential for ensuring the quality of the final product.
- Efficient Cooling Systems: Implementing a counterflow cooler can improve the cooling efficiency of the pellets. Proper cooling is crucial for reducing moisture content and preventing spoilage. Additionally, efficient cooling can enhance pellet durability and reduce breakage during handling.
- Effective Screening: Using a vibrating screen or similar equipment to remove fines and oversized pellets can improve the overall quality of the product. Ensuring a consistent pellet size enhances marketability and reduces waste.
7. Quality Control Measures
Implementing robust quality control measures throughout the production process is essential for maintaining product quality and optimizing costs.
- Regular Testing: Conducting regular tests on raw materials and finished pellets for key quality parameters, such as moisture content, density, and durability, helps identify issues early and allows for timely adjustments to the production process.
- Feedback Loops: Establishing feedback mechanisms that allow operators to report on the quality of the pellets can help identify trends and areas for improvement. This proactive approach can lead to ongoing efficiency gains over time.
8. Employee Training and Engagement
Investing in employee training and engagement is crucial for optimizing the production process.
- Comprehensive Training Programs: Providing thorough training for operators on the proper operation of the bagasse pellet machine, maintenance procedures, and quality control measures can enhance overall efficiency. Well-trained staff are better equipped to identify and resolve issues quickly.
- Encouraging Feedback: Fostering a culture of open communication where employees can provide feedback on the production process can lead to valuable insights and improvements. Recognizing and rewarding employees for their contributions can further motivate engagement.
Conclusion
Optimizing the production process of a bagasse pellet machine is essential for reducing costs and enhancing profitability. By focusing on raw material management, conditioning, pellet mill optimization, energy efficiency, cooling and screening, quality control, and employee training, producers can improve production efficiency while maintaining high-quality standards.As the demand for sustainable biomass energy and animal feed continues to grow, investing in the optimization of bagasse pellet production will be crucial for maintaining a competitive edge in the market. By implementing these strategies, producers can achieve significant cost savings and contribute to a more sustainable future.