Biomass pellet making machines are pivotal in converting various biomass materials into high-density fuel pellets, which serve as a renewable energy source. However, the efficiency of these machines directly impacts production costs, profitability, and overall sustainability. By optimizing the operational efficiency of a biomass pellet making machine, producers can significantly reduce costs while enhancing productivity. This article outlines key strategies for achieving this optimization.
1. Selecting High-Quality Raw Materials
The quality of raw materials used in pellet production is fundamental to the efficiency of the biomass pellet making machine.
- Moisture Content: The ideal moisture content for biomass materials typically ranges between 10% and 15%. Materials that are too wet can lead to poor pellet quality and increased energy consumption during the drying process. Conversely, overly dry materials can cause excessive wear on the machinery. Regularly testing and adjusting the moisture content of raw materials can improve pellet quality and reduce operational costs.
- Material Consistency: Using uniform raw materials helps maintain a steady production process. Mixing different types of biomass can lead to variations in pellet quality and machine performance. Ensuring that the raw materials are consistent in size and composition can enhance the efficiency of the pelletizing process.
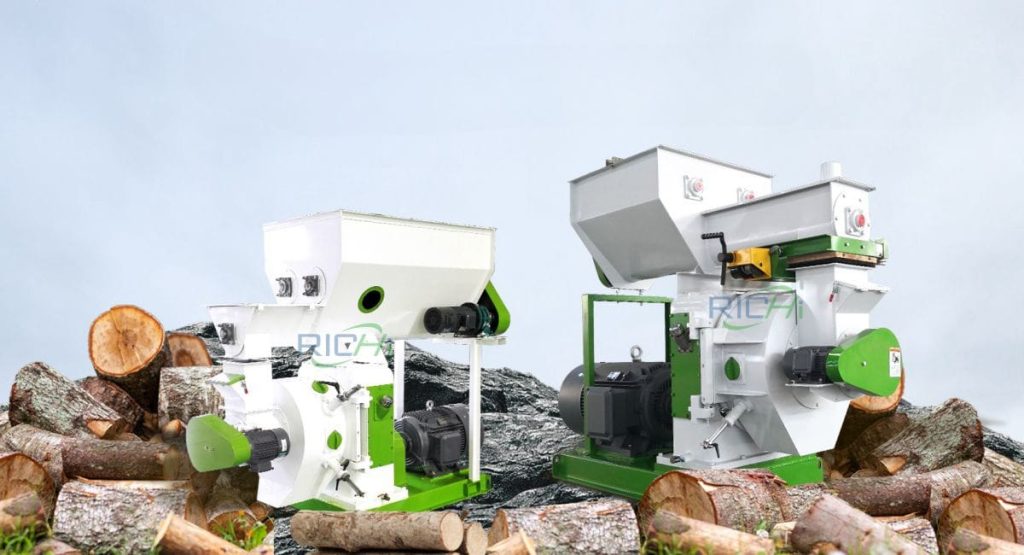
2. Proper Equipment Maintenance
Regular maintenance of the biomass pellet making machine is crucial for ensuring optimal performance and minimizing downtime.
- Routine Inspections: Conduct regular inspections of all machine components, including the die, rollers, and feeding system. Look for signs of wear and tear, and address any issues promptly to prevent further damage.
- Lubrication: Proper lubrication of moving parts reduces friction and wear, extending the lifespan of the equipment. Establish a routine lubrication schedule based on the manufacturer’s recommendations and the operating conditions of the machine.
- Cleaning: Keeping the machine clean is essential for maintaining efficiency. Residue buildup can impede the operation and lead to quality issues. Regularly clean the die and other critical components to ensure smooth operation.
3. Optimizing the Pelletizing Process
The pelletizing process itself can be fine-tuned to improve efficiency and reduce costs.
- Adjusting Die Settings: The die plays a crucial role in determining the size and density of the pellets. Adjusting the die settings to match the specific characteristics of the biomass being processed can lead to improved pellet quality and reduced energy consumption.
- Controlling Temperature: The temperature during the pelleting process affects the quality of the pellets. Monitoring and controlling the temperature can help achieve optimal conditions for binding the biomass fibers. If the temperature is too low, the pellets may not form properly; if it is too high, it can lead to degradation of the biomass and increased wear on the equipment.
- Feeding Rate Management: Ensuring a consistent and appropriate feeding rate into the pellet mill is essential for maintaining efficiency. An inconsistent feed can lead to fluctuations in pressure and temperature, negatively impacting pellet quality. Implementing automated feeding systems can help achieve a steady flow of material.
4. Energy Efficiency Improvements
Energy consumption is a significant cost factor in the operation of biomass pellet making machines. Implementing energy-efficient practices can lead to substantial cost savings.
- Using Energy-Efficient Equipment: When selecting a biomass pellet making machine, consider models that are designed for energy efficiency. Machines with advanced technology and optimized designs can reduce energy consumption while maintaining high production rates.
- Regenerative Systems: Incorporating regenerative systems that capture and reuse energy from the pelletizing process can significantly reduce overall energy costs. For example, using waste heat from the machine to dry incoming biomass can enhance efficiency.
- Monitoring Energy Usage: Regularly monitor energy consumption to identify areas where efficiency can be improved. Implementing energy management systems can help track usage patterns and highlight opportunities for savings.
5. Training and Skilled Labor
The efficiency of a biomass pellet making machine is also influenced by the skill level of the operators.
- Operator Training: Providing comprehensive training for operators on the proper use and maintenance of the pellet machine is essential. Well-trained operators are more likely to follow best practices, leading to improved efficiency and reduced operational issues.
- Continuous Education: Keeping operators updated on the latest technologies and practices in biomass pellet production can lead to ongoing improvements in efficiency. Encourage a culture of continuous learning and adaptation within the workforce.
6. Implementing Quality Control Measures
Quality control is vital for ensuring that the pellets produced meet the necessary standards, which can impact overall efficiency and costs.
- Regular Testing: Implement a regular testing schedule for the pellets produced to ensure they meet quality specifications. This includes testing for moisture content, density, and durability. Addressing quality issues promptly can prevent waste and reduce costs associated with reprocessing.
- Feedback Loops: Create feedback mechanisms that allow operators to report issues and suggest improvements. This can help identify inefficiencies in the production process and lead to actionable changes that enhance overall performance.
7. Utilizing Technology and Automation
Incorporating technology and automation into the production process can enhance efficiency and reduce costs.
- Automated Systems: Implementing automated feeding and monitoring systems can help maintain consistent production rates and reduce labor costs. Automation can also minimize human error, leading to improved pellet quality.
- Data Analytics: Utilizing data analytics tools can help monitor machine performance in real-time, allowing for proactive adjustments and maintenance. Analyzing production data can identify trends and areas for improvement, leading to enhanced efficiency.
Conclusion
Optimizing the operational efficiency of a biomass fuel pellet machine is essential for reducing costs and enhancing productivity. By focusing on the quality of raw materials, proper maintenance, optimizing the pelletizing process, improving energy efficiency, training skilled labor, implementing quality control measures, and utilizing technology, producers can significantly improve the performance of their pellet mills.As the demand for renewable energy sources continues to grow, maximizing the efficiency of biomass pellet production will be crucial for maintaining a competitive edge in the market. By investing in these optimization strategies, producers can achieve significant cost savings and contribute to a more sustainable future.